Mitsubishi Electric redevelops biomethane gas-to-grid injection unit
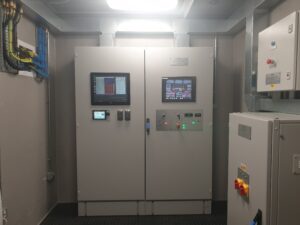
Sourcing a direct alternative to natural gas at scale is not yet feasible, according to Mitsubishi Electric. That is why supplementing supply at a local level with biomethane is becoming an increasingly popular solution.
The benefits of biomethane are well known – it offers similar thermal characteristics to natural gas, and can be produced almost anywhere in the world.
However, before grid integration into the network, the feed gas produced during the anaerobic digestion process needs to be verified to ensure it comes with Gas Safety Management Regulations. This is done using specialist integration units, such as those manufactured by Orbital Gas Systems – one of the UK’s largest system integrators in the energy industry.
“Central to the biomethane industry is the green transformation of gas supplies, a commitment firmly anchored in the principles of sustainability," said Chris Williams, head of engineering and digital technology at Orbital. "Recent fluctuations in the broader energy market have highlighted the significance of biomethane in enhancing the reliability of gas supplies."
With growing customer demand for more efficient, easy to use and sustainable gas distribution systems, the team at Orbital took the decision to redesign its original biomethane grid entry unit from the ground up.
“We’ve worked on a lot of national infrastructure projects, so we have a good understanding of balancing what the DNOs want with the needs of our own customers – whether that is the plant owner or an integration company managing the project on behalf of the end-customer," continued Williams.
At the heart of any grid entry unit lies the control system, which is not only responsible for the overall quality of the gas but, among other functions, the flow measurement and propane enrichment.
“The PLC and HMI in our original control system were functional, however they also presented some operational and service challenges that we wanted to rectify with our new grid entry unit,” he added.
“For example, it used a physical monitor which could only be accessed on-site, or via remote access software. This made it very difficult for more than one engineer or operator to access the data without getting in each other’s way. What’s more, it was becoming increasingly difficult to find engineers familiar with the technology and the security of the supply chain was starting to come into question.”
When it came to developing a new control system, Orbital, turned to industrial automation specialists, Mitsubishi Electric.
Orbital first started working with Mitsubishi Electric in 2018, as part of a telemetry system it was developing.
“Whilst that particular project didn’t make it to market, it did broker a really productive relationship between Orbital and Mitsubishi Electric,” said Williams. “As a result, the Mitsubishi Electric i-QR PLC and GOT HMI have become our preferred control system of choice, including on our new biomethane grid entry unit.”
The iQ-R PLC provided the Orbital engineering team with a user-friendly, intuitive programming environment in GX Works3, whilst the touchscreen interface of the GOT HMI allowed for easy navigation for critical viewing and trending parameters.
With security one of several key design criteria for the new unit, the PLC ensured any changing of control parameters, such as PID tuning, was only available to users with the correct access.
A final design criteria was ensuring the control system could be automated, with no manual intervention required to reset the grid entry unit. Not only could the iQ-R PLC facilitate this, but in doing so Orbital became the only manufacturer to ensure gas flow automatically resumed during normal operations after events such as gas quality excursions.
Ian Allcock, Orbital’s lead digital technology engineer, was closely involved in engineering the new biomethane grid entry unit: “A major challenge faced by our original control system was data collection and transfer. In contrast, the Mitsubishi Electric system made it much easier to collect and record data, logfiles were more reliable and the PLC and HMI were more robust.”
However, the biggest difference for Orbital customers lay in the web-based capabilities of the GOT HMI, which enabled a tangible improvement in alarming and troubleshooting.
“Unlike the previous system, the web-based platform allowed multiple stakeholders to securely login at the same time – either locally or remotely via a VPN. This made fault diagnosis much faster,” continued Allcock.
“It even helped us make more data available to the customer. We could now identify what caused an alarm to trip by taking a snapshot of all the data at the point it tripped. For example, if a valve shut off, we could look at the data snapshot and work backwards to identify the cause, such as the calorific value being too high. Ultimately, this led to a much faster fix for the customer and a definitive reduction in downtime.”
Orbital has subsequently installed its new biomethane grid entry unit at 10 sites throughout the UK.
Whilst the Mitsubishi Electric control system has improved the overall usability of the unit, it has also helped streamline maintenance and service activity.
“Because of Mitsubishi Electric’s global presence, it is very easy to source parts throughout the UK, even for remote sites,” concluded Williams. “There’s also a much higher number of software engineers who are familiar with the technology compared to other systems, so people can come in and hit the ground running.”
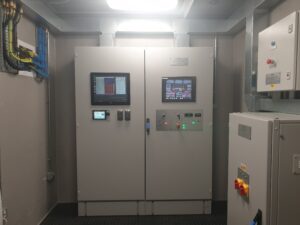