Automated in-line moisture monitoring increases productivity
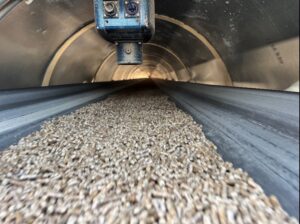
Incorporating the right combination of automation tools can help production facilities overcome challenges posed by outdated machinery and labour-intensive procedures that hinder overall productivity.
One key example is automated moisture monitoring, where the 'steel collar' worker automates mundane, repetitive, and time-consuming tasks, allowing valuable human resources to focus on more critical jobs and eliminate inefficiencies that hinder peak production.
When installed directly on the production line, automated moisture monitoring significantly reduces human error inherent in time consuming and out of date manual processes. Incorporating moisture measurement during production allows the user to create a closed-loop process and have full control over the production line. While several methods are available, the use of near-infrared (NIR) technology can produce a high return on investment (ROI).
Benefits of moisture content measurement equipment and processes
Moisture measurements are used throughout many manufacturing processes, from examining incoming raw materials, to ensuring final product quality and shipping weight. Moisture ranges outside of tolerance can inhibit the production process and even create wear and tear on other equipment. Each phase of the manufacturing process runs more efficiently and profitably with accurate moisture content.
In the past, many firms have relied on manual moisture testing and measurement methods, but these old school methods are notoriously subject to errors and are a known primary cause of many production issues. Manual moisture monitoring essentially requires a laboratory setup in a controlled environment. Samples need to be immediately sealed in plastic or glass jars once taken from the production line and taken for testing. The moisture content will naturally change every minute that passes once the sample is removed from the production line, throwing off the final results. Older manual testing methods (for example, ovens) often lose the ability to test samples accurately.
Moisture control systems automate and accelerate many of these mundane inspection-based quality tasks. Adding the automation of moisture detection throughout the production process can eliminate the frequent mistakes and allow for a closed loop process when tied directly into a programmable logic control (PLC) system. With critical points of production being monitored for moisture content, everything from the raw material to the finished product can be precisely monitored for accuracy and quality.
In addition, moisture measurement systems tied into the process controller can easily detect out of spec products so they can be dealt with immediately to ensure additional product is not affected. When issues are identified early, corrections can be made long before an imperfect or contaminated product reaches consumers.
Real-time process control with moisture detection provides true product data that can be used to improve operation efficiency. This reduces wasted effort and materials, and decreases the frequency of downtime, manual intervention, and defective goods. Real-time control of moisture leads to significant cost savings, in terms of energy, spoilage, down time, quality control rejects, and customer complaints. For processes that can be closely controlled using real-time measurements, in-line systems in feedback-loops often produce a high return on investment (ROI).
Automated in-line moisture measurement technologies
Several technologies are available for automated in-line moisture measurement. One such method that greatly improves quality is near-infrared (NIR) technology, which uses a simple light source for measurement.
NIR moisture measurement is a fast, non-destructive, non-contact method of measuring and controlling moisture content that offers clear advantages over the traditional methods, including ease-of-use, elimination of hazardous chemicals, and increased efficiency of product testing. With NIR analysis, all manual steps of collecting, drying and accurately weighing samples are eliminated. When incorporated throughout the production process, NIR technology greatly improves quality.
NIR moisture sensors give manufacturers the ability to adjust moisture levels on real-time information, lowering raw material and fuel costs, higher yields, and more uniform products. Allowing the moisture measurement to be automated with high and low alarms built into the system allows for personnel to focus on other aspects of the process while maintaining accuracy in moisture control. It reduces human error, increases plant efficiency from the automated process and frees up man hours for other tasks that cannot be automated.
Since NIR depends on light reflection, its one key disadvantage is associated with its use with products that are largely or completely carbon black. The technology still works but may require tweaking or adjustments.
In addition to NIR, other automated technologies are available. For example, microwave technology sensors are often used in wood biomass applications, but they tend to lose accuracy quickly and may not give the same results every time. Those reliant on accuracy to a specific percentage must steer away from microwave technology. Another option is nuclear technology. While extremely accurate, cost is a major disadvantage; nuclear options may be four to five times the cost of NIR technology.
NIR moisture measurement improves the pellet manufacturing process
Waste products are often turned into pellet fuel for heating electric power plants, schools, and homes. Wood pellets are made from compacted sawdust or other sawmill waste products, as well as palm kernel shells, coconut shells, rice husks, wheat, and grasses. Manufacturing wood pellets requires refining, drying and blending of wood waste prior to entering the pellet press. Measuring moisture throughout the wood pelletising process will produce pellets at a specific moisture percentage, preventing products that are too wet or too dry.
Nate Harris, president of Custom Pelleting Services, explained: “One metric that is often overlooked or, rather I should say undervalued, is the moisture rate of the biomass. I have found that changing the moisture percentage even by as little as 1 percent makes a noticeable difference in the pellet quality both in the durability and in the sheen.”
He added: “We have found that by using MoistTech’s IR3000 moisture sensors, we are able to make adjustments to the programming of the dryer system to provide a more consistent biomass moisture rate in real time that directly correlates to a higher production capacity and a better quality pellet.”
Improve quality by incorporating automated moisture measurement
Quality and consistency are crucial when it comes to maintaining a manufacturing line. Implementing an automated moisture control sensor instantly reduces waste and energy costs as well as improves the efficiency of the line. In many cases, manufacturers can achieve a very favorable ROI.
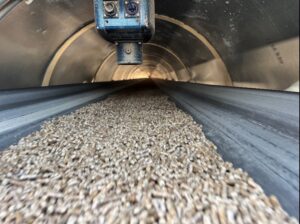