AMANDUS KAHL presents plants for more economical wood processing
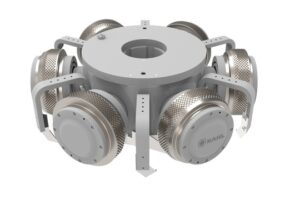
At Ligna 2025, AMANDUS KAHL will show how energy and costs can be saved along the entire production chain: from wet grinding with the pan grinder mill, energy-efficient drying with the fabric belt dryer, pelleting with the Eco Roll and optional Distamat control system, to cooling with a belt unit.
For 50 years, Ligna has been the world's leading trade fair for the woodworking and wood processing industries.
“Linking people, driving innovation” is also the central promise in the anniversary year, which attracts international industry representatives to Hannover from May 26 to 30. At booth F57 in hall 26, AMANDUS KAHL will show how machine operators can make a valuable contribution to sustainable and efficient wood processing – one of the main topics of this year's trade fair.
Pan grinder mill: energy-efficient wet grinding
As an alternative to wet grinding with a hammer mill, the pan grinder mill from AMANDUS KAHL allows particularly energy-efficient grinding of the wood. The special defibration across the fiber direction ensures a uniform particle size. Depending on the desired pellet quality, subsequent dry grinding may not even be necessary. This not only saves time, but also up to 50 percent of the energy that would otherwise be required for dry grinding – a decisive factor for economical and sustainable pellet production.
Fabric belt dryer: effective recovery of waste heat
The AMANDUS KAHL fabric belt dryer also focuses on saving resources in the next processing step. Due to the low inlet air temperatures of less than 120°C, waste heat from combined heat and power plants can be used for energy-efficient drying of the wood chips. The result is uniform residual moisture of 10-12% with minimal energy consumption. In addition, the close-meshed synthetic fabric belt of the dryer filters the exhaust air and reduces the dust particles to less than half of the legal limits.
Pelleting with Eco Roll and Distamat: 25% increase in efficiency
The energy efficiency of KAHL flat die pellet mills can be further improved with two optional technologies. With the new Eco Roll technology, the crushed and dried product is compacted in two steps, instead of applying the entire required pressing force in a single step. This reduces energy consumption to only 40-45 kWh per ton of softwood. With a production volume of 50,000 tons and an electricity price of 20 cents per kWh, up to 1,250 MWh of electricity can be saved. At the same time, production capacity increases by up to 25%.
The Distamat technology also contributes to resource-efficient pelleting. As an option, it can be integrated into the electronic automatic pellet mill regulation system (EAPR) to maintain a constant gap between the pan grinder rollers and the die. This extends the service life of wear parts, while reducing energy consumption and minimising production downtime.
In the downstream KAHL belt cooler, the hot pellets are gently and efficiently cooled to 5-10 °C above ambient temperature.
With the combination of pan grinder mill, fabric belt dryer, pellet mill with Eco Roll and Distamat and belt cooler, AMANDUS KAHL offers a fully integrated, energy-efficient pellet production line.
Visitors to Ligna 2025 will be able to experience these cost-saving technologies first hand.
In addition to the pellet mill 65-1500, the supplier of complete plants will present the new Eco Roll and a hologram showing the Distamat control system.
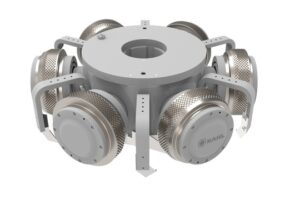